La prova di non combustibilità UNI EN ISO 1182 è un test che permette di valutare la resistenza alla fiamma di un materiale collocato all'interno di un fornetto a "tiraggio" naturale. La macchina di test ha una geometria speciale caratterizzata da un lungo cono di imboccatura al fornetto posizionato nella parte inferiore. Il cono rovesciato ha diametro uguale a quello del forno (75mm) nella parte alta e un diametro di soli 10 mm nella parte inferiore, l'aria viene movimentata verso l'alto dalla parte calda del forno che genera una depressione all'altezza del foro da 10mm. Il tiraggio naturale per sua natura è fortemente influenzabile da molti parametri, non a caso nella norma si menziona l'esigenza di posizionare l'equipaggiamento di test lontano da correnti d'aria. Il flusso d'aria attraverso l'imboccatura del cono è bilanciato in modo da garantire l'adeguato apporto di ossigeno (favorendo la combustione) senza asportare eccessivo calore (evitando di rallentare così la combustione). Come ARGO abbiamo simulato la portata d'aria della prova in condizioni ideali di tiraggio naturale. Questi valori sono particolarmente utili per monitorare la ripetibilità di questi test rapportandoli ai dati sperimentali ottenuti posizionando un anemometro all'ingresso del cono di aspirazione naturale.
ENGLISH VERSION COMING SOON - FOR ANY INFO WRITE ME @ Questo indirizzo email è protetto dagli spambots. È necessario abilitare JavaScript per vederlo.
Leggi tutto: Simulazione della prova di non combustibilità UNI EN ISO 1182
Nonostante la grande attenzione mediatica (es. Industria4.0) i reali benefici dell’innovazione e della cultura del miglioramento continuo fanno fatica ad arrivare nelle imprese italiane. Il motivo di questa scarsa adesione risiede principalmente nel tessuto industriale italiano, come noto, composto in larga maggioranza da Piccole Medie Imprese (PMI).
Cosa significa dire che le piccole imprese non innovano? Bisogna precisare, le piccole imprese italiane sono spesso parte di un indotto o in ogni caso di un mercato globale, pertanto esse non sono totalmente stagne all’innovazione: i prodotti si sono aggiornati, sono più performanti e ottimizzati concorrendo a mantenere alta la percezione di manifattura italiana di qualità.
Allora in quali aspetti le PMI tendono a non innovare? L’innovazione latita prevalentemente nei processi produttivi, rimasti tecnologicamente indietro rispetto ai prodotti stessi. Di conseguenza emerge che le stesse procedure manifatturiere di 20 anni fa non sono più applicabili ai prodotti odierni. In questo contesto il vero tallone d’Achille della PMI italiana è la cultura del “si è sempre fatto così”.
Perché viene trascurata l’innovazione nei processi ? Non esiste un unico motivo quanto piuttosto un habitat in cui il “si è sempre fatto così” trova terreno fertile. In primis in una realtà piccola è oggettivamente difficile avere a disposizione un ventaglio di competenze industriali sempre aggiornate e sufficientemente vaste. Spesso le decisioni sia tecniche sia amministrative vengono prese da una singola persona, generalmente il titolare, la quale con il passare del tempo diventa meno recettivo e sensibile ad innovare. In nessun caso si può dire che la scelta di non innovare è consapevole, nella maggior parte dei casi non sono semplicemente noti e a portata l’ammontare dei costi che la stagnazione porta.
Qual è l’impatto sull’azienda di un processo non ottimizzato? Diverse analisi dimostrano che non innovare e trascurare l’ottimizzazione dei processi equivale a produrre in non-qualità. Non è per nulla semplice definire con certezza l’ammontare delle perdite finanziare associate alla scarsa innovazione. Esse sono specifiche per ogni azienda e rare sono le regole comuni. Esistono però dei valori medi, estrapolati da studi universitari o consortili, sull’incidenza media. Una PMI che ha investito poco o nulla nell’innovazione di processo negli ultimi 10 anni o più può arrivare ad avere una percentuale di scarti effettivi anche superiore al 30%. I danni derivati da un numero elevato di pezzi non conformi sono molteplici e comprendono le misure correttive in corso d’opera, il valore aggiunto perso ed il danno di immagine con conseguente perdita di quote mercato.
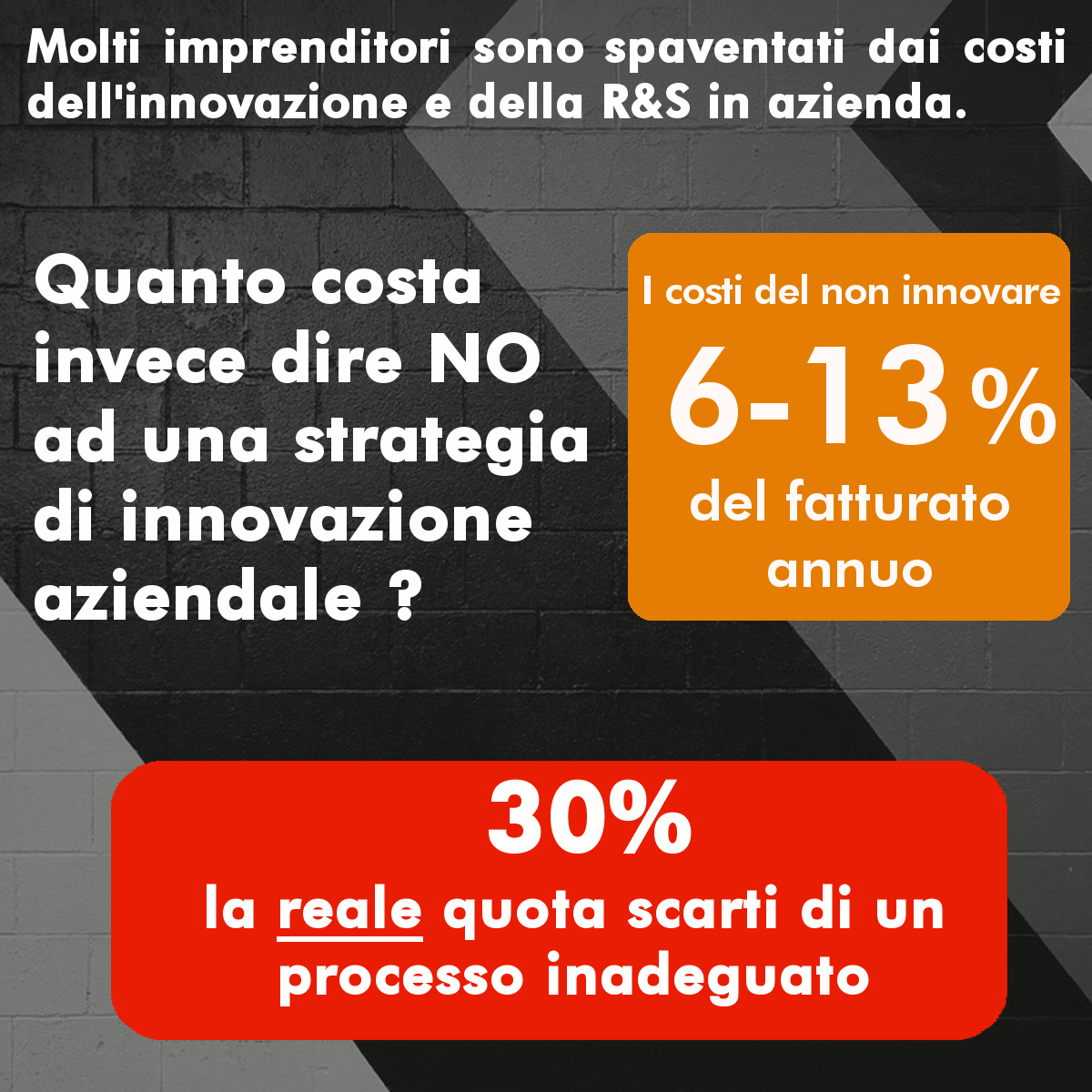
Quindi a quanto ammontano i costi del non innovare? Produrre per inerzia, senza innovazione o strategie di risoluzione problemi costa all’azienda un valore compreso tra il 6% ed il 13% del fatturato dell’azienda. Un valore non di rado superiore all’utile stesso dell’azienda! Considerato pari a circa 850 miliardi di € il fatturato delle PMI in Italia e che la % di aziende dove l’innovazione e l’ottimizzazione non trovano spazio sia ancora troppo estesa emerge chiaramente la quantità di profitto non realizzato.
Quanto costa innovare? L’innovazione di un processo non ha valori prestabiliti, dipende dal singolo caso specifico e può variare di uno o due ordini di grandezza, non esiste un valore medio. Spesso molti imprenditori chiudono le porte dell’azienda al pensiero di investire in innovazione cifre dell’ordine di alcune decine di migliaia di € a fronte di risparmi calcolabili in centinaia di migliaia di €. La base di tutto questo è ancora una volta la non consapevolezza dei costi non preventivati sostenuti in produzione per raggiungere il risultato “teorico” previsto in progettazione.
Non c’è limite alle spese di innovazione? Diversamente dal pensiero di certe culture tecnologico-entusiaste esiste un chiaro limite all’investimento in innovazione, ottimizzazione e R&S. Esiste una soglia oltre la quale la misura di innovazione ha un costo superiore al vantaggio economico prodotto. Spesso un’errata valutazione degli strumenti da impiegare per innovare porta ad investimenti cospicui che non sono ammortabili nel medio periodo o addirittura non sostenibili.
Come si innova e come si stabilisce un budget? L’approccio all’innovazione deve essere condotto da esperti in Innovation Management (IM) o esperti in ricerca industriale, possibilmente con l’appoggio di centri di ricerca o Università. Queste figure specifiche sono spesso assenti nelle PMI, per i motivi sopracitati, e pertanto è più conveniente per le aziende reperirle esternamente sotto forma di consulenza. Una consulenza che deve però procedere in totale sincronia con i vertici aziendali, stimando sulla base dell’esperienza e con i responsabili di produzione l’ipotetico incremento in produttività, definendo così l’entità della sacca di inefficienza e calibrando di conseguenza le misure degli investimenti.
Questa guida è una traduzione in italiano, un po' rivisitata, dell'ottima “Tips and tricks in OpenFOAM” scritta dai ragazzi di www.wolfdynamics.com che ringrazio personalmente.
This is just a translation, if you are looking for the english version take a look at the complete original guide written by the guys of www.wolfdynamics.com
Capitolo #1 : la mesh – trucchi e suggerimenti
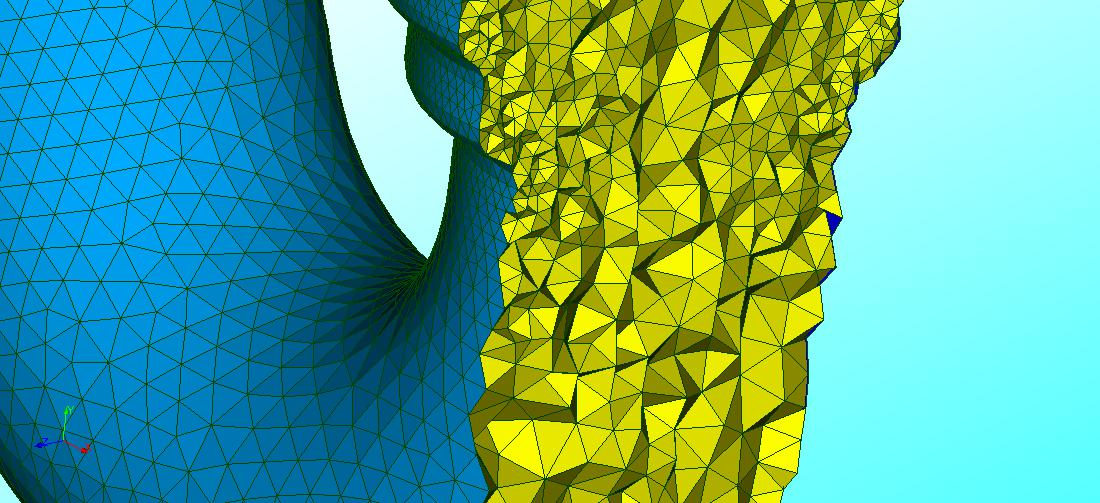
A livello generale per qualsiasi software CFD ai volume finiti la mesh, o griglia di calcolo, è un elemento fondamentale per la buona riuscita della simulazione. Ricordate che il computer per definizione è un moltiplicatore, pertanto: spazzatura in ingresso = spazzatura in uscita, oppure rileggendolo in forma positiva: buona mesh = buoni risultati. A fronte dell’esperienza maturata negli anni non mi stancherò mai di ripeterlo in questa guida: per ottenere risultati di qualità serve una mesh di altrettanta buona qualità, una mesh non idonea porta a risultati falsati, quindi totalmente inutili, o addirittura “all’esplosione” della simulazione per mancata convergenza. Provare a correggere la simulazione attraverso schemi di risoluzione più robusti può migliorare la situazione ma non è in grado di risolverla completamente. Il consiglio è sempre quello di rigenerale la mesh (anche se costa ore di calcolo) e quindi procedere con la simulazione. Ma come faccio a sapere se la mia mesh è idonea?
checkMesh
Ogni programma ha il suo strumento di analisi e pertanto anche OpenFOAM ha la sua utility: checkMesh che è possibile lanciare dal terminale aperto nella cartella della simulazione. checkMesh, come dice il nome stesso, controlla la mesh presente nella cartella e fornisce un report finale che indica la presenza o meno di errori e la loro tipologia.
checkMehs inoltre è in grado di salvare tutte le celle “difettose” (inclusi le facce e i punti problematici) in un dataset all’interno della cartella constant/polyMesh/sets/. Convertendoli in formato VTK attraverso il comando foamToVTK è possibile aprire questo dataset in paraFoam o paraview e visualizzare direttamente cosa “non piace” a OpenFOAM della vostra mesh.
Linee guida generali per una mesh a scopo CFD.
Queste regole sono valide anche per altri software, cito ad esempio Code_Saturne sviluppato dall’EDF, in quanto sono “naturale conseguenza” delle dinamiche risolutive del metodo ai volumi finiti. Facendo una breve lista:
- Minimizzare il più possibile la non-ortogonalità tra le celle
- Evitare rapporti di forma troppo elevati nelle celle, specialmente vicino alle condizioni al contorno
- Evitare fattori di crescita (growth rate) troppo elevati in quanto portano a gradienti di dimensione cella troppo forti (zone a celle molto piccole vicino a celle troppo grandi)
- Evitare inoltre forti gradienti dimensionali in direzione normale alle condizioni al contorno vicino agli ingressi e all’uscita del fluido
- Come regola generale nelle pareti sottili: discretizzare lo spessore facendo in modo che vi siano almeno 3 o più celle. A questo scopo tornano molto utili le funzioni layer-mesh definite anche viscous-layer durante la formulazione della mesh.
Suggerimento finale : renumberMesh
Prima di lanciare una simulazione può essere molto utile eseguire il comando renumberMesh. Questa utility rinumera la mesh compattandone la banda e rendendola quindi più facilmente risolvibile. Ciò significa che il risolutore lineare sarà in grado di procedere più velocemente (almeno per i primi time-step) ed è pertanto un’ottima abitudine da eseguire sempre dopo il checkMesh e prima dell’inizio del calcolo, specialmente per le mesh di grandi dimensioni.
Leggi tutto: Guida pratica ad OpenFOAM - #1 mesh